-
- News
- Books
Featured Books
- pcb007 Magazine
Latest Issues
Current IssueThe Growing Industry
In this issue of PCB007 Magazine, we talk with leading economic experts, advocacy specialists in Washington, D.C., and PCB company leadership to get a well-rounded picture of what’s happening in the industry today. Don’t miss it.
The Sustainability Issue
Sustainability is one of the most widely used terms in business today, especially for electronics and manufacturing but what does it mean to you? We explore the environmental, business, and economic impacts.
The Fabricator’s Guide to IPC APEX EXPO
This issue previews many of the important events taking place at this year's show and highlights some changes and opportunities. So, buckle up. We are counting down to IPC APEX EXPO 2024.
- Articles
- Columns
Search Console
- Links
- Events
||| MENU - pcb007 Magazine
35 Years of HDI Fabrication Processes and Obstacles for Implementation
December 4, 2017 | Happy Holden, I-Connect007Estimated reading time: 2 minutes
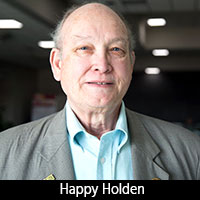
Introduction
The electronics industry is the world’s largest and most robust market. It is also a bulwark of American creativity, with Silicon Valley as its origin and fortress. The SIA Roadmap is still pushing the size of wafer transistors smaller and smaller, with the resulting faster rise times and need for finer pitch. But silicon needs a mounting platform and the printed circuit and organic IC package will be needed to create working products.
For North America, there is a growing need for more HDI capability. Some of the reasons for the slower adoption of HDI fabrication in N.A. may rest with four obstacles: Defining density needs; EDA tools not providing increased functionality; process controls for fabricating reliable microvias; and bare-board/ICT solutions once HDI is assembled.
A wakeup call may be too strong a term, but it is time to seriously consider what you are going to do about HDI. The adage “offshore can’t handle our technology” is out of date. Offshore (or Asia) can now do 24-layer multilayers, laser-drilled HDIs, fine lines (2-mil traces and spaces), flip chip packages, pure gold, hard gold, low loss materials, RF, buried capacitance, mixed dielectrics, etc. The current production analysis of HDI technology released by TechSearch International in “HighDensity Microvia Substrates: Markets, Applications and Infrastructure−Updated” shows that Asia had 86% of the HDI business in 2016−2017.
As you can see in Figure 1, North America is a mere 5% of the total. TechSearch predicts that HDI will grow to $18.6 billion by 2020. Now you might ask, why is this so? The two main uses for HDI are for portable products like cellular phones and camcorders and for finepitch IC packages. It just happens that Japan, Korea and Taiwan make a lot of these products and we don’t. In fact, at the Electronics Circuits World Conference 14, companies like Samsung have been working on new lower-cost laser HDI technologies using thermoset resins. This eliminates the need for lamination presses and lowers the material costs in the production of microvias.
Lately, my time has been monopolized by OEMs asking about the most cost-effective way to use the new 0.5 mm BGAs. Many of these are digital signal processors (DSP) and custom ASICs in the 457 to 1384 I/Os range. These are being produced in the millions now and are going into all sorts of sophisticated servers, networking and telecom products. These industrial products will now form the third platform for HDI. These products also make up a majority of the high value-added electronics produced in North America.
The reason for the increase in fine-pitch BGA activity can be seen in Figure 2. In 2016, BGAs are approaching the costs of quad flat packages and complex (high pin count) packages now cost less than one cent per pin. With package prices like that, all OEMs are considering how to use them in their new products.
To read the full version of this article which appeared in the November 2017 issue of The PCB Magazine, click here.
Suggested Items
KYZEN’s Adam Klett to Keynote at SMTA Electronics in Harsh Environments Conference
05/07/2024 | KYZEN'KYZEN, the global leader in innovative environmentally friendly cleaning chemistries, announced today that KYZEN’s Director of Science, Adam Klett, PhD will present as a keynote speaker at the SMTA Electronics in Harsh Environments Conference. The event is scheduled to take place May 14-16, 2024 at the Technical University of Denmark in Copenhagen, Denmark.
Altus Equips SSTL with Advanced Cleaning Technology for Electronics
05/07/2024 | Altus GroupAltus Group, a leading supplier of capital equipment for the electronics manufacturing industry, has announced the successful installation of an advanced PCBA cleaning system at Surrey Satellite Technology Limited (SSTL).
GPV's Handover of Refurbished Factory Building
05/07/2024 | GPVOn 6 May 2024, Bjorn Fiskers, MD at GPV Electronics TH in Thailand and his team were handed the keys to our refurbished factory building, adding another 7,000 sqm to our current 15,000 sqm electronics factory. Our electronics factory in Thailand will comprise of a total of 22,000 sqm.
New Yorker, Major League Electronics Sign New Franchised Distribution Agreement
05/06/2024 | New Yorker Electronics Co.New Yorker Electronics, global distributor of electronic components, recently announced a new franchised distribution agreement with Major League Electronics, renowned manufacturer of interconnect products.
AT&S Brings High-Tech to the Museumsquartier
05/06/2024 | AT&SAT&S, as a “MQ goes Green” partner, has prepared special highlights for the occasion: Visitors aged eight and above can embark on an interactive journey through the fascinating world of microelectronics.