Electrolube to Launch New Thermal Management Solutions at electronica
October 30, 2018 | ElectrolubeEstimated reading time: 3 minutes
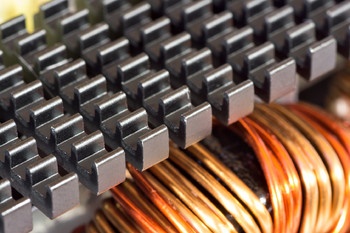
Electrolube will have a strong presence at this year’s Electronica event (November 13-16, Munich, Germany), with two separate stands across the exhibition complex. In hall A2 on stand 437, the company will be showing a range of thermal management products, including its innovative new phase change materials.
Providing an effective thermally conductive interface between a component and its heat sink is essential to achieving long life and reliability. For many, thermal greases continue to be the material of choice in this area, but interesting new phase change materials are now offering a more stable alternative with real ease of application.
Phase change materials soften significantly once heated above their phase change temperature and perform as well, or sometimes even better than a traditional thermal grease. These materials can also offer long-term stability and are highly suited to thermally challenging applications where product life expectancy and reliability may be critical. Such applications include LED lighting, automotive electronics and remotely located wind power inverters.
Electrolube recently added two new thermally conductive phase change materials to its thermal management product portfolio: TPM350 and TPM550, and these will be the main highlight of the company's exhibit in Hall A2. TPM350 has a thermal conductivity of 3.5W/m.K and becomes workable at approximately 50°C. At this 'activation' temperature it changes state to become a lower viscosity material, minimising contact thermal resistance and improving thermal conductivity. Once it cools, it reverts back to its original state. The material’s advanced formulation ensures minimal contact thermal resistance.
TPM550 has a higher thermal conductivity of 5.5W/m.K and an activation temperature of 45˚C. In common with the TPM350 product, TPM550 is thixotropic, which prevents flow outside of defined interfaces. Both TPM350 and TPM550 can be reworked and their low specific gravity means that more applications can be served per kilogram of the materials, reducing production costs.
The new phase change materials are silicone-free, have an operating temperature range of -40 to +125˚C and are RoHS-2 compliant. TPM350 and TPM550 are screen printable and, while they do contain small amounts of solvent to improve wettability on application, this rapidly evaporates following application to leave the solid phase change material on the substrate. Both products are formulations comprising an advanced polymer matrix and a dispersion of highly thermally conductive fillers that determine the material’s phase change temperature with great accuracy.
Further new thermal management products to be shown this year from Electrolube's broad range of thermally conductive resins, includes the flame retardant, thermally conductive, two-part ER2220 epoxy, which has been specifically designed to meet increasing demands for efficient thermal dissipation. With its high thermal conductivity of 1.54 W/m.K, ER2220 offers ease of processing whilst providing superior protection and performance across a wide range of applications, including those in the rapidly expanding LED lighting industry.
Electrolube will also have an exhibit in hall B4 on stand 315, where the emphasis will be on solutions for the escalating automotive electronics market. Playing host on both stands, Electrolube’s materials and technology experts will make themselves available throughout the show to answer visitors’ queries and suggest possible solutions to materials and application problems.
About Electrolube
Electrolube, a division of H.K. Wentworth Limited, is a leading manufacturer of specialist chemicals for electronics, automotive and industrial manufacturing. Core product groups include conformal coatings, contact lubricants, thermal management materials, cleaning solutions, encapsulation resins and maintenance and service aids.
The extensive range of electro-chemicals at Electrolube enables the company to offer a ‘complete solution’ to leading manufacturers of electronic, industrial and domestic devices, at all levels of the production process. Through collaboration and research, the company is continually developing new and environmentally friendly products for customers around the world and their commitment to developing ‘greener’ products has been endorsed by the ISO 14001 standard for the highly efficient Environmental Management System in place at the company.
Winners of the Queen’s award for Enterprise 2016, Electrolube is represented in over 55 countries with an established network of subsidiaries and distributors. By offering genuine security of scale and a reliable supply chain, the company is able to deliver a truly tailored service.
Visit I-007eBooks to download your copy of Electrolube micro eBook today:
The Printed Circuit Assembler's Guide to...Conformal Coatings for Harsh Environments
Suggested Items
SMC Korea 2024 to Highlight Semiconductor Materials Trends and Innovations on Industry’s Path to $1 Trillion
04/24/2024 | SEMIWith Korea a major consumer of semiconductor materials and advanced materials a key driver of innovation on the industry’s path to $1 trillion, industry leaders and experts will gather at SMC (Strategic Materials Conference) Korea 2024 on May 29 at the Suwon Convention Center in Gyeonggi-do, South Korea to provide insights into the latest materials developments and trends. Registration is open.
Groundbreaking Ceremony Marks the Beginning of a New Era for Newccess Industrial; The Construction of the MINGXIN Building
04/12/2024 | Newccess IndustrialOn a clear and sunny day in March, the groundbreaking ceremony for the MINGXIN Building took place in Shenzhen, China. This moment marked the official commencement of construction for a project that will reshape the semiconductor materials industry.
The Need for a Holistic Global Sustainability Standard
04/10/2024 | Michael Ford, Aegis SoftwareNo one can deny that the resources of our fragile planet are finite. The environment seems like a third party, subject to constant degradation. We’re acutely aware of the effects of pollution on our climate, and despite our “throw-away” culture, recycling and recovery of materials has remained relatively expensive, even as we use more energy just to survive.
iNEMI Publishes Four Roadmap Topics
04/04/2024 | iNEMIThe International Electronics Manufacturing Initiative (iNEMI) announces the availability of the first roadmap topics in the new iNEMI Roadmap format. Printed circuit boards, sustainable electronics, smart manufacturing, and mmWave materials and test are now available online.
Insulectro’s 'Storekeepers' Extend Their Welcome to Technology Village at IPC APEX EXPO
04/03/2024 | InsulectroInsulectro, the largest distributor of materials for use in the manufacture of PCBs and printed electronics, welcomes attendees to its TECHNOLOGY VILLAGE during this year’s IPC APEX EXPO at the Anaheim Convention Center, April 9-11, 2024.